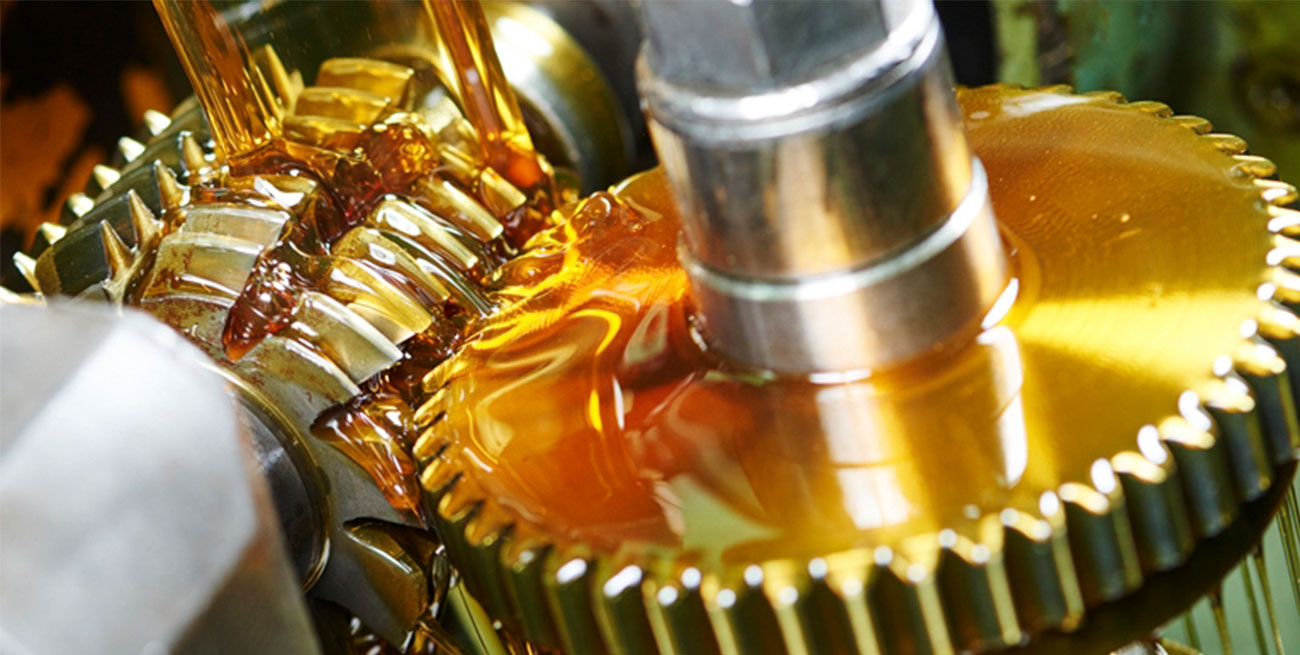
09 Apr روغن های هیدرولیک و ويژگی های آنها
روغن هیدرولیک همچون روغن های دیگر از اختلاط “روغن پایه” و مواد افزودنی تولید می شود. که می تواند با توجه به نوع روغن پایه و مواد افزودنی، کاربرد های مختلفی در سیستم های گوناگون داشته باشد.
روغن هیدرولیک را می توان پر مصرف ترین روغن صنعتی نامید، و از اینرو با توجه به مصرف بالا و کاربردهای متنوع و شرایط کاری گوناگون، این روغن نیز از تنوع بالایی برخوردار است.
در واقع روغن هیدرولیک در یک سیستم نقش انتقال دهنده انژی را بازی می کند و در صورتی که این روغن دچار مشکل شود، این وظیفه بخوبی انجام نشده و سیستم با اختلال یا توقف در کارکرد روبرو می گردد.
بطور کلی روغن های هیدرولیک بر اساس استاندارد ISO 6743 به سطوح کیفیت زیر تقسیم بندی می شوند:
1- HH: روغن پایه معدنی بدون مواد افزودنی. این اولین نسل از روغن های هیدرولیک بود.
2- HL: با اضافه کردن مواد افزودنی ضدزنگ و ضد اکسیداسیون نسل جدیدی از این روغن ها بوجود آمد که به این گروه روغن های گردشی نیز گفته می شود.
3- HM: با اضافه کردن مواد افزودنی ضد سایش به روغن های HL روغن های هیدرولیک جدید تولید شد که در حال حاضر پر مصرف ترین روغن های هیدرولیک هستند.
4- HV: با بالا بردن شاخص گرانروی روغن های هیدرولیک HM ، این سطح کیفیت بدست آمد، که برای کار کرد در محدوده دمایی وسیع مناسبند.
5- HG: این روغن ها که به روغن هیدرولیک ماشین ابزار معروفند، با خاصیت چسبندگی که دارد، در سیستم های کشویی رفت و برگشتی از سیستم به بیرون پرتاب نمی شوند.
این تقسیم بندی سطوح کیفیت یکی از معروف ترین طبقه بندی روغن های هیدرولیک است. ولی استانداردهای دیگر نیز در روغن های هیدرولیک تعریف شده اند که می توان استانداردهای زیر را نام برد:
DIN 51524, Cetop RP 91 H, Afnor nfe, Cincinnati Milacron, …
بطور کلی وظایفی که از یک روغن هیدرولیک انتظار می رود، روانکاری، انتقال نیرو، کاهش اصطکاک و سایش، محافظت از زنگ زدگی اجزاء سیستم و سازگاری با تمام اجزاء سیستم است.
دسته دیگر از روغن های هیدرولیک هستند که به روغن سیالات هیدرولیک ضد آتش معروف هستند. البته این بدین معنی نیست که این سیالات در مجاورت با آتش شعله ور نمی شوند، بلکه آنها در مجاورت با آتش دیرتر شعله ور شده و در برابر انتشار شعله مقاومت می کنند. این دسته از روغن ها معمولا در مکان هایی که احتمال آتش سوزی زیاد است (مانند درب کوره های ذوب فلزات) مورد استفاده قرار می گیرند.
این روغن ها نیز به چهار دسته اصلی تقسیم می شوند:
1- HFA : امولسیون های روغن در آب
2- HFB: امولسیون آب در روغن
3- HFC: سیالات آب گلایکول
4- HFD: مایعات سینتتیک
نکته:
آنچه در کار کردن با روغن های هیدرولیک باید در نظر داشت این است که روغن های هیدرولیک مانند “روغن های توربین” به شدت به آلودگی هایی که وارد آنها می شوند حساس هستند و خصوصیات فیزیکی و شیمیایی آنها در اثر آلودگی و ایجاد شرایط سخت کاری برای روغن دچار مشکل خواهد شد. همچنین در هنگام انتخاب روغن برای سیستم هیدرولیک، با استفاده از مشاوره کارشناسان روانکاری، روغن مناسبی را انتخاب کنید و با رعایت موارد و نکات کاربردی برای مصرف، تعویض، سرریز و از همه مهمتر مراقبت وضعیت (CM) روغن، به افزایش عمر آن و سلامت تجهیزات کمک کنید و در نهایت بتوانیم به نتیجه مطلوب کاهش هزینه های روانکاری دست پیدا کنید.
روغن توربین چیست؟
روغن توربین یک روانکار از دسته روغن های گردشی است که باید دارای خصوصیات فیزیکی و شیمیایی ویژه ای برای انجام وظایف مورد نظر در توربین باشد.این وظایف عبارتند از:
1- روانکاری یاتاقان ها، چرخ دنده ها و کوپلینگ ها.
2- انتقال حرارت و خنک کاری در یاتاقان ها.
3- عملکرد مناسب هیدرولیکی.
4- محافظت از زنگ زدگی و سایش.
برای انجام این وظایف در توربین ، روغن توربین باید دارای خواص فیزیکی و شیمیایی ویژه ای باشد تا بتواند برای مدت طولانی در شرایط مناسب در توربین کار کند. این خصوصیات عبارتند از:
1- جلوگیری از اکسیداسیون.
2- جلوگیری از خوردگی و سایش.
3- جداپذیری از آب و هوا.
4- جلوگیری از کف کردن.
برای تامین این خصوصیات سازندگان روغن با استفاده از روغن پایه مناسب و مواد افزودنی ویژه روغن توربین را تولید می کنند.
در ترکیب روغن توربین ، حداکثر 3% از مواد افزودنی استفاده می شود، این امر نشان می دهد که تامین بخش عمده ای از خصوصیات این روغن بر عهده روغن پایه است و مواد افزودنی تقویت کننده خصوصیات روغن پایه هستند. به همین منظور سازندگان روغن برای انتخاب روغن پایه مورد استفاده در روغن توربین دقت زیادی به عمل می آورند.
حال ببینیم زمان کارکرد روغن توربین چقدر است؟
آنچه در مقاله زمان کارکرد روغن هیدرولیک چقدر است؟ گفته شد در مورد روغن های توربین نیز صدق می کند. ولی در توربین ها به دلیل اهمیت و حساسیت کار، دقت بیشتری از طرف سازندگان توربین به مسایل مربوط به روغن و شرایط نگهداری آن شده است.
سازندگان توربین بر اساس نوع توربین (گاز، بخار، آب) شرایط خاصی را برای نگهداری روغن توربین در نظر می گیرند، برای مثال در روغن مورد استفاده در توربین های بخار و آب خاصیت جداپذیری از آب در درجه اهمیت بالایی قرار دارد، در حالی که در توربین های گاز این خاصیت در اولویت قرار ندارد. ولی خصوصیتی مانند عدد اسیدی در تمام توربین ها اهمیت دارند و سازندگان برای توربین های تولیدی خود حدود مشخصی را برای این مشخصه تعریف می کنند.
در هر صورت بهترین کار برای نگهداری از روغن توربین استفاده از توصیه سازندگان توربین و مشاوره متخصصین روانکاری در برنامه CM است.
نکته بسیار مهم در کارکرد با روغن توربین رعایت مواردی است که متخصصین روانکاری برای جلوگیری از آلودگی روغن توربین به مصرف کننده ارایه می دهند. چرا که بارها دیده شده که به دلیل عدم رعایت این موارد علاوه بر از بین رفتن روغن، آسیب های جدی نیز به یاتاقان های توربین وارد شده که برطرف کردن آن نیاز به وقت و هزینه زیادی داشته است.
روغن کمپرسورهای تبریدی
پرسش: آیا دمای نقطه ریزش در یک روغن کمپرسور تبریدی باید از دمایی که کمپرسور ایجاد می کند کمتر باشد ؟
در روغن های کمپرسور خصوصیتی به نام نقطه توده شدن (Floc Point) اهمیت بسیار مهمی دارد. این نقطه بالاترین دمایی است که در مجاورت سیال تبریدی در روغن مواد مومی موجود در آن به حالت جامد در می آیند و ظاهر روغن را راکد می کنند. پایین بودن نقطه توده شدن مشخصه مطلوبی برای روانکارهای سیستم برودتی است.
این مشخصه با نقطه ریزش (Pour Point) (پایین ترین دمایی که در آن روغن هنوز جاری است) متفاوت است. در واقع نقطه توده شدن از نقطه ریزش بالاتر است .
حال با دانستن مفهوم این دو مشخصه می توانیم در انتخاب روغن کمپرسور تبریدی دقت کنیم.
در انتخاب روغن کمپرسور باید دقت شود که نقطه توده شدن روغن از دمایی که توسط کمپرسور ایجاد می شود کمتر باشد، تا در حین کار به دلیل اختلاط روغن با سیال تبریدی، مواد مومی بصورت جامد در نیایند. چرا که این اتفاق باعث وارد شدن خسارت به کمپرسور و توقف کار می شود.
نتیجه دمای نقطه ریزش در یک روغن کمپرسور از دمایی که کمپرسور ایجاد می کند کمتر است.
روغن کمپرسور
کمپرسور وسیله ای است که انرژی مکانیکی را به تراکمی برای تامین گاز یا هوای فشرده تبدیل می کند.
کمپرسورها بطور کلی به دو دسته اصلی تقسیم می شوند:
1- کمپرسورهای دوار Rotating
2- کمپرسورهای رفت و برگشتی Reciprocating
این دو دسته نیز خود به انواع گوناگون تقسیم بندی می شوند که در این مقاله به آنها پرداخته نمی شود.
نوع دیگری از تقسیم بندی کمپرسورها بر اساس گاز مورد تراکم است که آنها را به سه دسته زیر تقسیم بندی می کند:
1- کمپرسورهای هوا
2- کمپرسورهای گاز
3- کمپرسورهای سرد
کمپرسورها در صنایع مختلف بخصوص صنایع پتروشیمی و گاز بطور گسترده ای کاربرد دارند. در واقع کمپرسورها در این صنایع جریان اصلی خط تولید را بطور مداوم حفظ می کنند و اهمیت بسیار بالایی برای این صنایع دارند. از این رو نگهداری این تجهیزات در شرایط مطلوب و کارایی مناسب در درجه اهمیت بالایی قرار دارند.
یکی از موارد بسیار مهم در کمپرسورها استفاده از روغن کمپرسور مناسب در آنها است.
روغن کمپرسور نیز مانند روغن های دیگر از دو بخش اصلی روغن پایه و مواد افزودنی تشکیل شده است که روانکاری، خنک کاری، آب بندی و جلوگیری از خوردگی و سایش از مهمترین وظایف عمومی این روغن ها به شمار می روند.
با توجه به تنوع زیاد کمپرسورها، تعریف سطوح کیفیت روغن برای تمامی آنها در یک استاندارد امکان پذیر نیست ولی معروف ترین سطح کیفیت تعریف شده برای کمپرسورهای رفت و برگشتی بر اساس استاندارد DIN 51506 به شکل زیر است :
VB , VBL , VC , VCL , VDL
خصوصیات این سطوح کیفیت با طراحی روغن های کمپرسور جدید به ترتیب از چپ به راست بهبود پیدا کرده اند.
این سه خصوصیت عبارتند از:
1- مقدار مواد ضد اکسداسیون.
2- تمایل به تولید کک و مواد صمغی.
3- کیفیت روغن پایه
برای انتخاب روغن مناسبی که بتواند این وظایف را در یک کمپرسور انجام دهد به چند عامل باید توجه کرد.
1- نوع کمپرسور:
انواع مختلف کمپرسور شرایط کارکرد متفاوتی با هم دارند در نتیجه تاثیر آنها بر خواص روغن نیز یکسان نخواهد بود.
2- نوع عملکرد کمپرسور:
به شرایط کاری کمپرسور بستگی دارد.
3- نوع گاز مورد تراکم:
گازهای مختلف می توانند بر روی روغن تاثیر گذار باشند. از اینرو انتخاب روغن سازگار با گاز مورد استفاده در کمپرسور اهمیت بسیار بالایی دارند و در صورتیکه این نکته رعایت نشود امکان بروز مشکلات بسیار جدی برای روغن و کمپرسور و درنتیجه خسارت سنگین به کارخانه وجود دارد. این موضوع بطور ویژه در کمپرسورهای تبریدی که با گازهای سرد کننده مختلفی کار می کنند مورد توجه قرار می گیرد.
4- توصیه سازنده:
این موضوع در انتخاب روغن یکی از مهمترین مسایل به شمار می رود.
بطور کلی در صنعت، برای کمپرسورها از روغن هایی با تنوع بسیار بالا استفاده می شود، که می توان از روغن های کمپرسور، موتور، توربین و روغن های کمپرسور تبریدی نام برد.
روغن های نامبرده هرکدام بنا به ویژگی های خاصی که دارند می توانند در برخی از انواع کمپرسورها کارایی داشته باشند و نیازهای روانکاری آنها را تامین کنند.
روغن های مربوط به کمپرسورهای سرد کننده به دلیل نوع خاص کاربرد و ویژگی گازهای سرد کننده در دمای کارکرد آنها، با روغن های کمپرسورهای دیگر اختلاف قابل توجهی دارند.